Pneumatic Cylinder Seals and Materials: How They Impact Performance
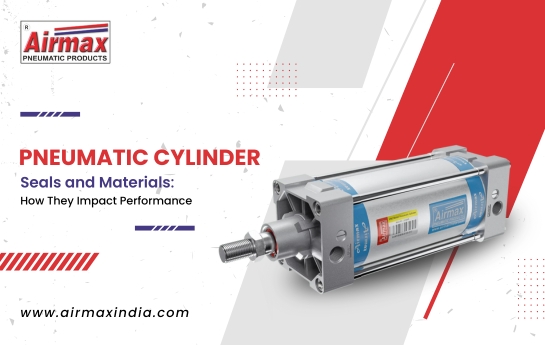
Pneumatic cylinders are essential components in modern automation systems, powering everything from manufacturing lines to packaging equipment. But what keeps these cylinders working smoothly and efficiently? The answer lies in pneumatic cylinder seals and the materials used in their construction. These often-overlooked parts play a crucial role in ensuring airtight operation, reducing wear, and extending the cylinder’s overall lifespan.
In this blog, we’ll explore the types of pneumatic air cylinder seals, materials used, and how they directly impact cylinder performance across various industries.
Types of Seals used in Pneumatic Cylinder
Pneumatic Air cylinder seals are designed to prevent air leakage, maintain pressure, and keep out contaminants. There are several key pneumatic cylinder seal types, each serving a specific function:
Rod Seals:
Used at the cylinder head, rod seals prevent air from escaping along the piston rod· In brands like Airmax, these seals are designed to handle dynamic movements and varying pressures.
Piston Seals:
Located inside the cylinder, air cylinder piston seals ensure that compressed air remains on one side of the piston, helping it to generate force· High-quality piston seals for pneumatic cylinders from Airmax improve efficiency and lower energy costs.
Wiper Seals (Scrapers):
These seals protect the internal components by scraping off dust, dirt, and moisture from the piston rod before it re-enters the cylinder.
Cushion Seals:
Cushion seals slow down the piston at the end of its stroke, reducing impact and extending component life. Piston seals vs rod seals differ mainly in function, while piston seals control internal airflow, rod seals focus on preventing external leakage.
Piston Seals vs Rod Seals in Pneumatic Cylinder
Piston and rod seals have distinct functions:
Within the cylinder, piston seals function. To maintain the necessary air pressure, they seal the piston’s two sides. Rod seals operate around the rod, outside the piston. As the rod moves, they keep air from escaping.
Consider this: rod seals ensure that no air escapes during movement. In contrast, piston seals maintain the air inside the chamber under control· When both are used correctly, your cylinder will operate effectively and without losing pressure.
Learn & get insight about “How to Calculate Stroke Length“
Common Seal Materials & Their Properties
Choosing the right material for pneumatic cylinder seals is critical to the application’s success· Here are the most commonly used materials and their benefits:
Nitrile (NBR): A cost-effective choice for standard applications. It offers decent wear resistance and air sealing.
Viton (FKM): Available on request from Airmax, Viton is suitable for high-temperature and chemical environments.
Polyurethane (PU): Known for excellent wear resistance and durability, making it ideal for tough conditions.
EPDM: Best for water-based or steam applications due to its moisture and heat resistance.
PTFE (Teflon): A premium choice for chemical resistance and low friction performance.
Each material provides a unique balance between sealing ability, durability, and environmental compatibility.
Cylinder Body Materials & Their Impact
Not just the seals, but the cylinder’s body material also affects performance:
Aluminum: Lightweight and corrosion-resistant, commonly used by Airmax for standard cylinders.
Stainless Steel: Ideal for food and pharmaceutical applications due to its hygienic properties.
Carbon Steel (WCB): Durable and budget-friendly, suitable for general-purpose industrial use.
Brass/Composite: Used in niche applications where specific properties are needed.
Temperature & Pressure Compatibility
Pneumatic seals must be compatible with the cylinder’s operating conditions. For example, Viton seals are essential in high-temperature environments, while NBR may fail in such settings. Proper material selection prevents air loss, hardening, or swelling of seals under varying pressures and temperatures.
Friction & Wear Considerations
Using incompatible materials can lead to excessive friction, causing heat buildup and premature seal wear. This not only affects performance but also increases maintenance downtime. Low-friction materials like PTFE help ensure smooth motion and longer seal life.
Also know about “How to measure Cylinder Bore Sizes“
Application-Specific Material Selection
Each industry has unique requirements. Here’s what to consider:
Food Industry: Use stainless steel cylinders with FDA-approved seals like EPDM or PTFE.
High-Temperature Environments: Opt for Viton or metal-constructed cylinders.
Dusty or Abrasive Conditions: Polyurethane seals with wipers prevent dust intrusion.
Water or Corrosive Media: EPDM or PTFE seals with stainless steel or brass bodies perform best.
Conclusion
The performance of pneumatic air cylinder seals depends heavily on both the Seal type and material compatibility. From rod and piston seals to the body construction of the cylinder itself, every element contributes to air-tight, efficient, and long-lasting operation. Whether you’re selecting a cylinder for automation, food-grade applications, or harsh industrial conditions, always choose seal and material combinations suited to your environment and trusted manufacturers like Airmax pneumatics to ensure reliability.
For expert guidance or to request a custom solution, feel free to Contact Us today.